FAQ Sensors
Each sensor has is optimal frequency range. This is related to laws of physics: more windings for example give better output voltage at low frequencies; more windings however cause a higher self-induction at higher frequencies. A fluxgate is insensitive against frequency changes, however the sensitivity is lower compared to coils. At long periods, where the amplitudes are high, this is an advantage, because the coils drops down with \(\left.dB \middle./ \right.dt\) Above periods of 30s the sensitivity of the fluxgate is to low for the small amplitudes but the frequency is still high enough for the coils to produce a good output voltage.
Chopper
The chopper is a special stabilizer for an amplifier in order to amplify low frequency signals with less noise. However in case the sampling frequency comes closer (or above) the chopper is causing noise (or is seen if the frequency is above).
In automatic mode all software will switch on the chopper for sampling rates at 512 Hz and lower.
Sensors with chopper (MFS-06e and MFS-07e) naturally devide the timeseries in two parts, the HF part (chopper off) and the LF part (chopper on).
The cross over between chopper on/off is around 100 Hz (above 100 Hz chopper off data is better).
Additionally the sensor switches a high-pass filter a 0.5 Hz. At least @10s period you have no data.
Now, the processing software has the strategy to create 4x bands by filtering.
Therefore the recording frequencies should be spaced by 16x
For a MFS-06e you would like to record 16kHz (4kHz filtered) that easily covers the chopper off part and interpretation down to 100Hz.
For chopper on you continue with 512Hz or 256Hz or 128Hz as long you need to reach your target depth.
You can check the chopper switching by intentionally switching the the chopper on for a 64 kHz recording (using the web interface); you must see the rectangular chopper switch around 2 kHz. The result depends on the system (send the chopper signal) AND the coil (must switch the chopper).
Recording 4 kHz with Chopper ON leads to an increased noise level around a factor of 3 - 5 for frequencies above 512 Hz. Under normal (or better) activity this is acceptable.
In case your spectra will be evaluated up to 1 or 1.5 kHz ( f_sample/ 4) you are just before the dead band.
Using the default settings of the ADB board the LF ADC blocks frequencies above 1800 Hz.
Assuming sub-jobs (32x continuous and 4 kHz bursts) you can stack the 4 kHz busts recorded several times. In Europe for example the AMT activity can reach
good levels around 02:00 in the morning hours.
Lost Data
Some user may use their own special job lists - and finally set the chopper wrong.
Basically the data can NOT be recovered because in HF mode (chopper off) the coils “does not see” lower frequencies and is very noisy below 1s.
At 100 seconds the sensitivity is already 30 to 50 times less with chopper off - so no data is expected at all.
One can help out to manipulate the standard calibration files (check, mix & add) with these two special low calibration data sets:
Chopper OFF LF MFS-06 calibration MFS06190_LF
Chopper OFF LF MFS-07 calibration MFS07028_LF
For your software you can try to understand this code snippet :
...
vector<double> fin, f_off_theo;
...
std::complex<double> trf
for (auto &f : fin) {
this->f_off_theo.push_back(f);
p1 = (f / 4.) * im;
p2 = (f / 8192.) * im;
p3 = (f / 0.72) * im;
p4 = (f / 25000.0) * im;
trf = 1. * 0.8 * ( (p1 / ( 1. + p1)) * (1. / (1. + p2)) * (p3 / (1. + p3)) * (1. / (1. + p4)) );
this->ampl_off_theo.push_back(abs(trf) / f);
this->phase_grad_off_theo.push_back(std::arg(trf) * 180. / M_PI);
}
that is for the low frequencies an approximation - not more! :
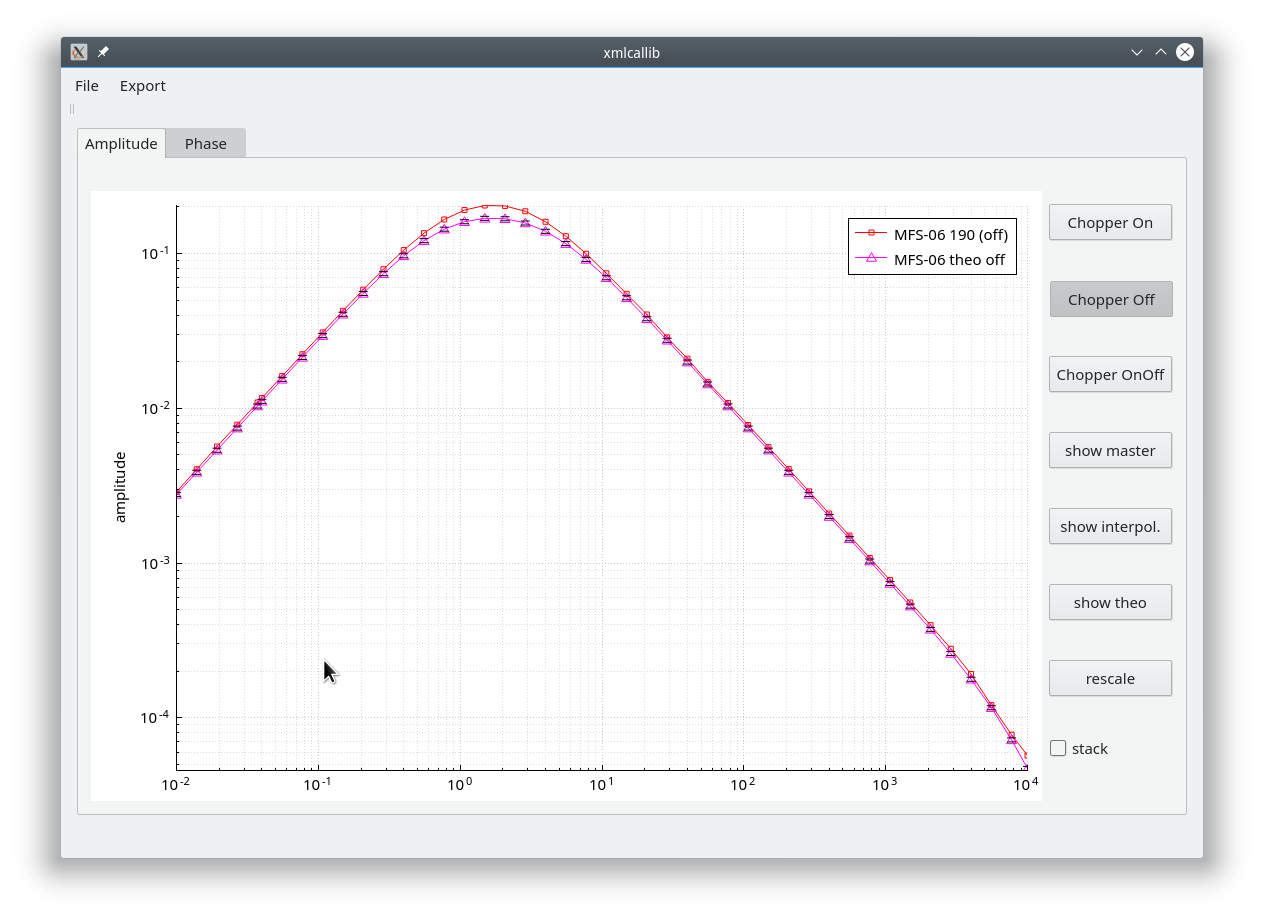
It is not guaranteed that YOUR coils matches like show above; another example:
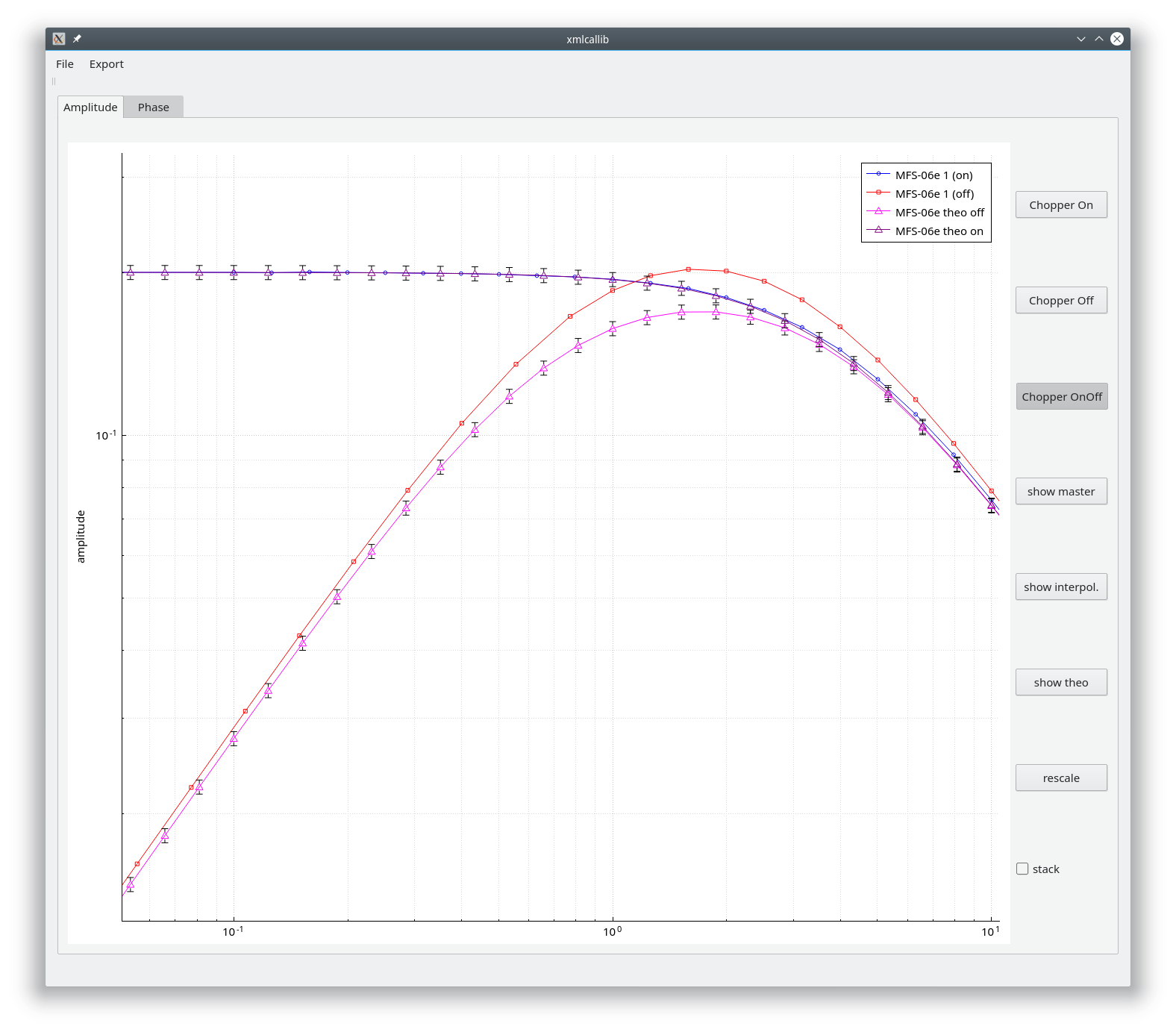
again: the coil is tuned to meet the theoretical calibration for chopper on at 10s.
Further issues: If you work with ProcMT or other software the software may not use the “wrong settings”. For ProcMT for example you must create / extend the “chopper off” section for each calibration and put the cal files into the ./cal folder. In the processing instructions (libmtx_calibration) you must have <set value=”auto” key=”calibration_type”/>, otherwise the manually created calibration files will be ignored.
MFS-06e vs MFS-07e
MFS-06e better than MFS-07e
chopper on lower 100 Hz
chopper off lower 512 Hz
This is only important for institutes using both coils.
Other comments are here How long do I have to record?
Frequency Ranges
A frequently ask question is: which sensor to use for a target depth of 3km?
Answer: depends on the conductivity of the layers above.
Time equals conductivity * depth.
At 100s on a conductive sedimentary basin we reach 3km of depth; on a resistive continental shield we are in 15km depth. And - to make it more interesting - some mountains can me quite conductive.
So you have to discuss with your geologist what you can expect at your target area first.
The second question is: does the coil “stop” at that frequency?
Answer: no.
When you compare MFS-07e and MFS-06e at 100s the noise level of the MFS-06e is three times better. Both record MT signals, with one difference:
If the MT activity is good and the area reasonable quite (as we have in Chile for example), both coils deliver good results.
In Germany however during low activity (Kp index) and medium noise levels, you definitively go for the MFS-06e.
Also the recording time plays a role: for short recordings and many site movements you may prefer the MFS-07e (and you may be interested in the more shallow parts).
For CSAMT you take the MFS-07e.
For MT with preference below 1 kHz you take the MFS-06e.
Remark: … company x says: “our coils are recording 10,000s … 20,000s … we get 1000s a day … “
… yes! And I am Santa Claus. Ref. to How long do I have to record? for the one hand.
On the other hand: under very good conditions our coils can record 10,000s and get data for interpretation for 1000s in one day. (10,000s with coils)
Does it help you? The problem is … you almost never have these excellent conditions
For 4096 s here in Germany we record typically between 5-7 days.
Performance overview coils
max |
opt max |
opt min |
min |
|
SHFT-02e |
250 kHz |
250 kHz |
5 kHz |
1 kHz |
MFS-07e |
50 kHz |
30 kHz |
10 Hz |
1000 s |
MFS-06e |
10 kHz |
4 kHz |
4096s |
10 000 s |
MFS-10e |
10 kHz |
1 kHz |
4096s |
4096 s |
FGS-03e |
30 s |
100 s |
20 000s |
100 000s |
Cables
length |
type |
max |
min |
5 m |
buffered |
500 kHz |
1 s |
10 m |
buffered |
128 kHz |
1 s |
50 m |
standard |
10 kHz |
10 000 s |
Hence that in most cases the standard cable can transfer up to 32 kHz. However on resistive ground and/or high contact resistivity this may NOT valid.
Calibration
At our calibration facility we tune and calibrate the induction coils.
At the first step the coil is tuned to the sensitivity 0.2 V/(nT*Hz) and 90° phase.
After that the transfer function is measured again: at the low end naturally theoretical and measured transfer function do meet. Above 512 Hz the coils are becoming more individual and the measured calibration must be used (below the theoretical fits vs. measured):
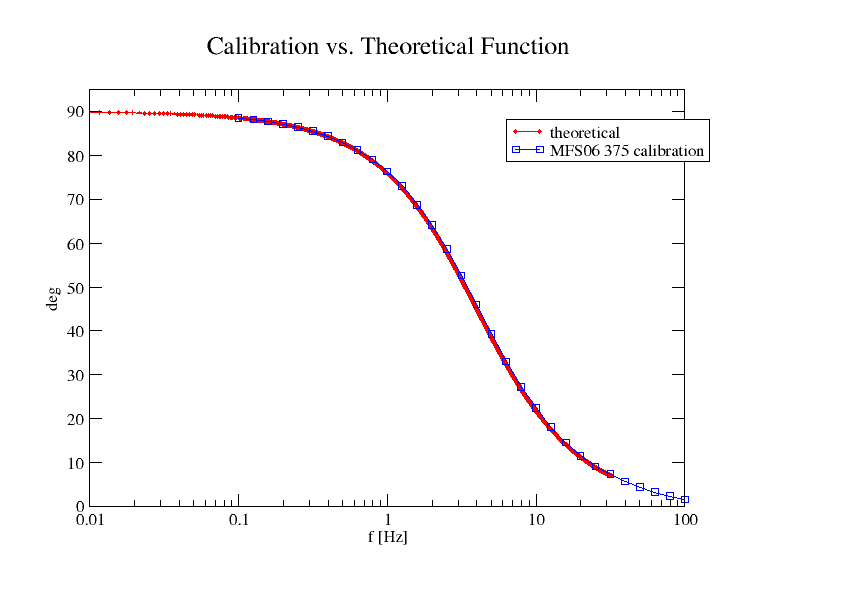
The default in the software is to extend the last measured value with the theoretical function.
The MFS coils are very stable and smooth in their calibration and not dependent on the field strength:
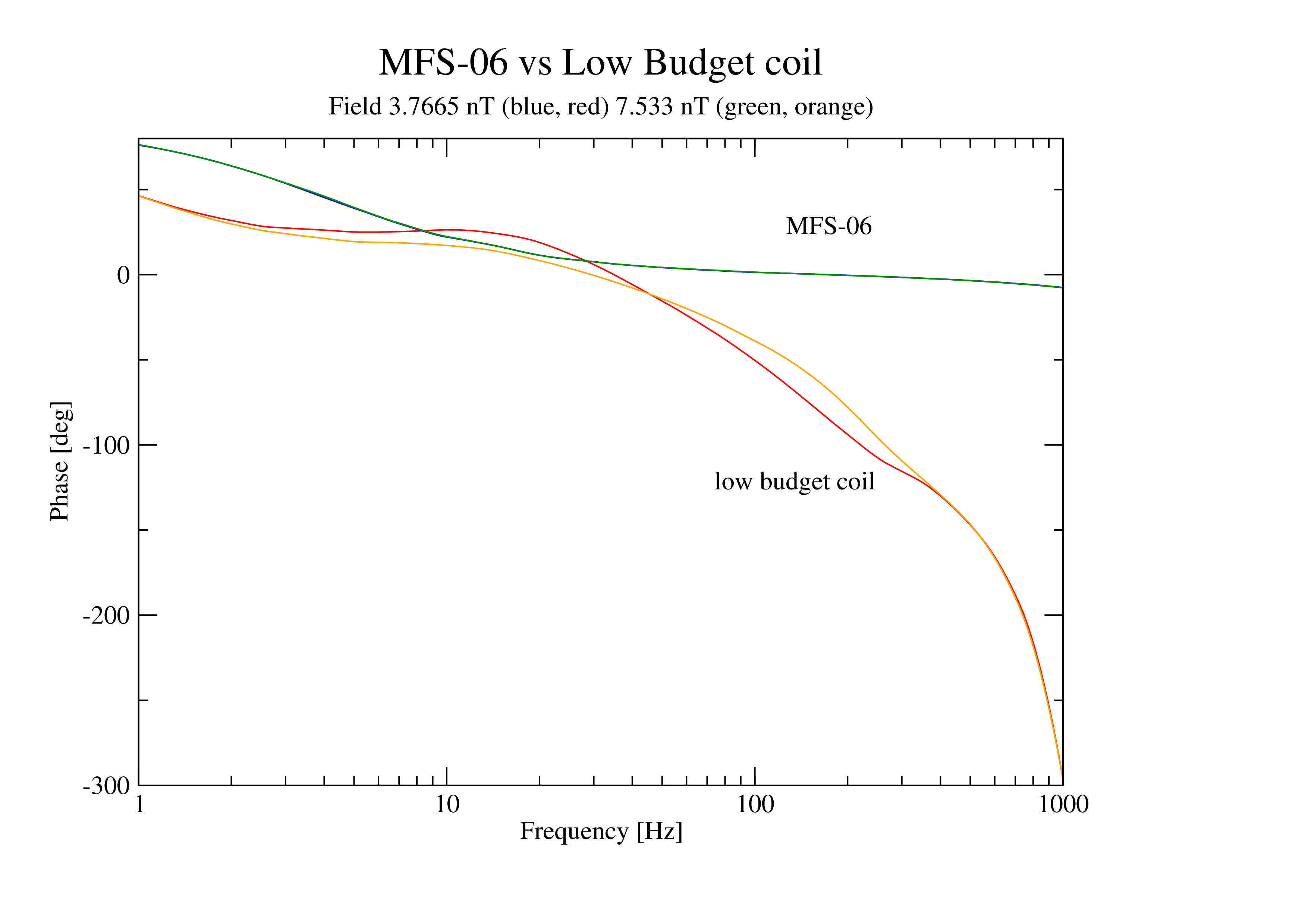
you see that blue and green are the same for the MFS coil; the low budget coils shows a amplitude dependency (which can not be corrected).
The calibration lasts for 10 years and more. This can be verified with the Insitu Coil Calibration Tool
Maximum Cable Length
The max. H cable length is 100 m.
We recommend to use 20 m.
The cable length can be extended up to 100 m. On request only. Only for f <= 4096 Hz.
There is a slight damping ab 4 kHz - but this “transfer function” has to be corrected by the user.
More critical howver is that the sensor detection may not work above 100 m. The digital signal of the \(I^2 C\) bus is smoothed out and not readable.
For the electric field +/- 50 m (== 100m total in one direction) is sufficient.
I do NOT need to unreel the E cable in case there is not enough space.
However: taking the full length of the cable gives you a “noise free amplification by nature”.
Additionally the part of the self-noise of the electrode gets less compared to the signal amplitude. For
the ADU system it does not matter if you have 4x gain and 50m or 8x gain and 30m.
Waterproof
The connectors are waterproof.
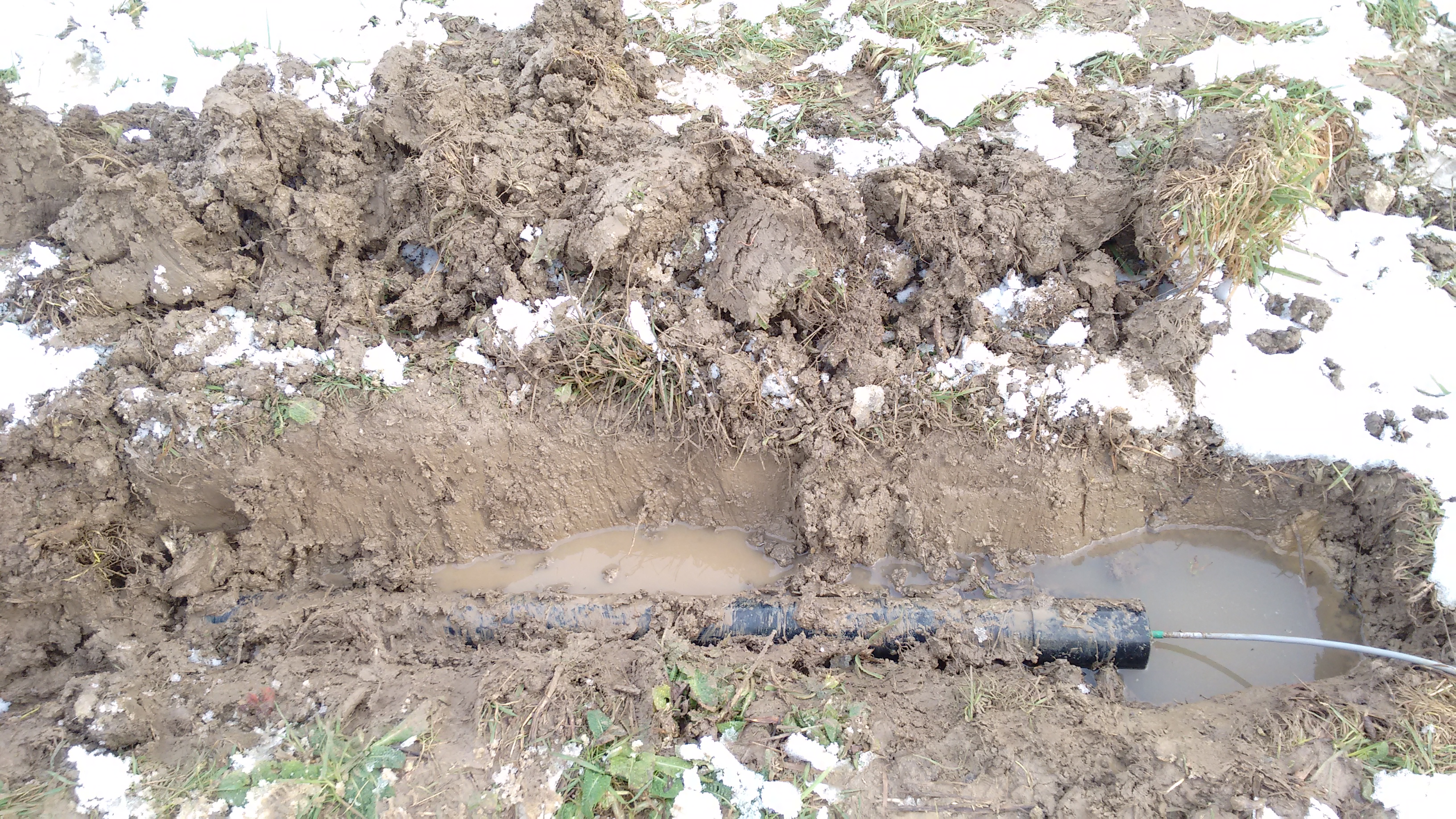
Do not pull the connectors when removing the coil.
The ADU is waterproof when the lid is closed. Sensors can be connected, sure.
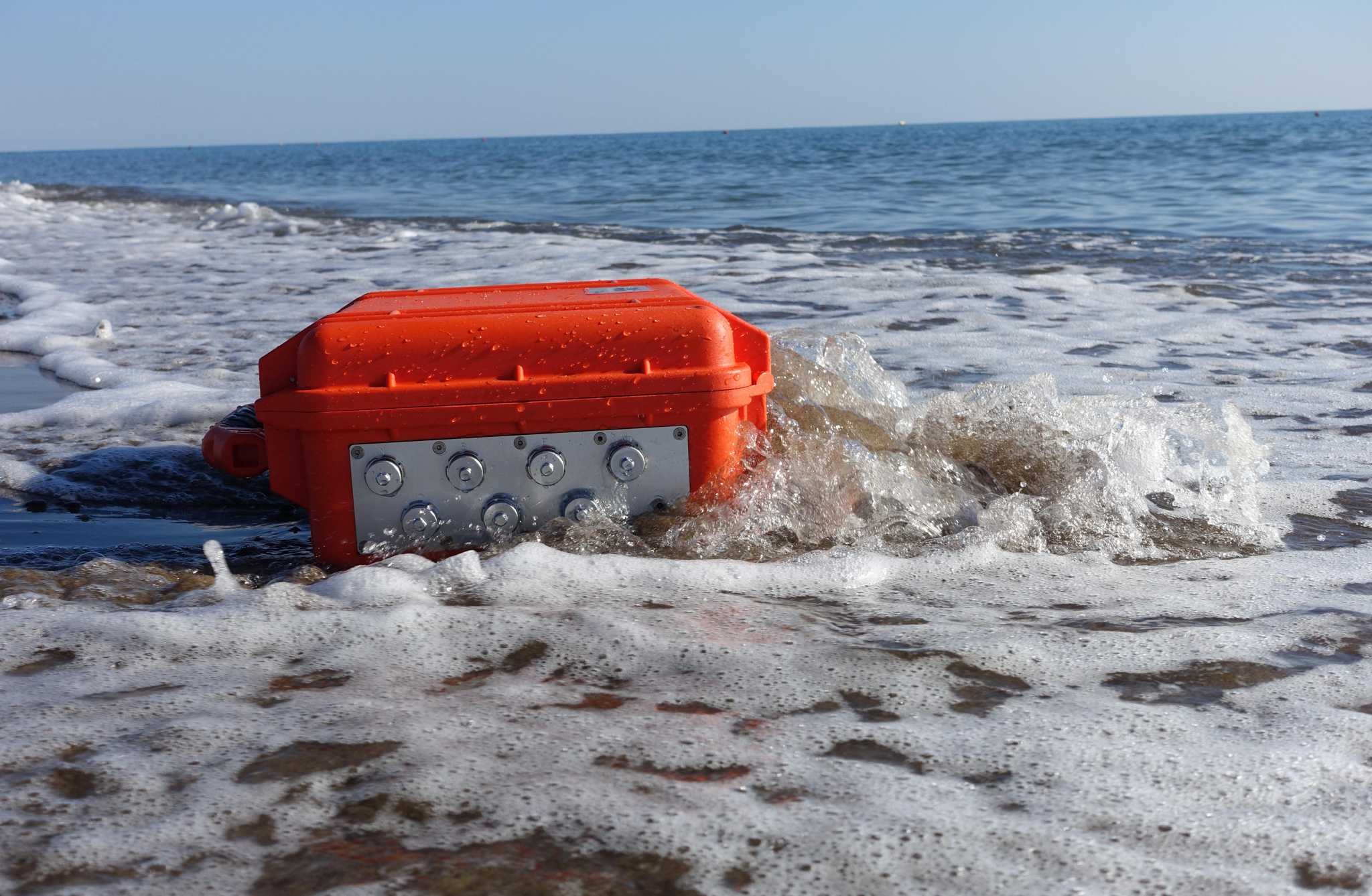
Replacing the Electrodes
The lifetime of PbPbCl2 electrodes is around 12, 18 max. 24 months. They simply getting older, even when not used!
You can see the alteration:
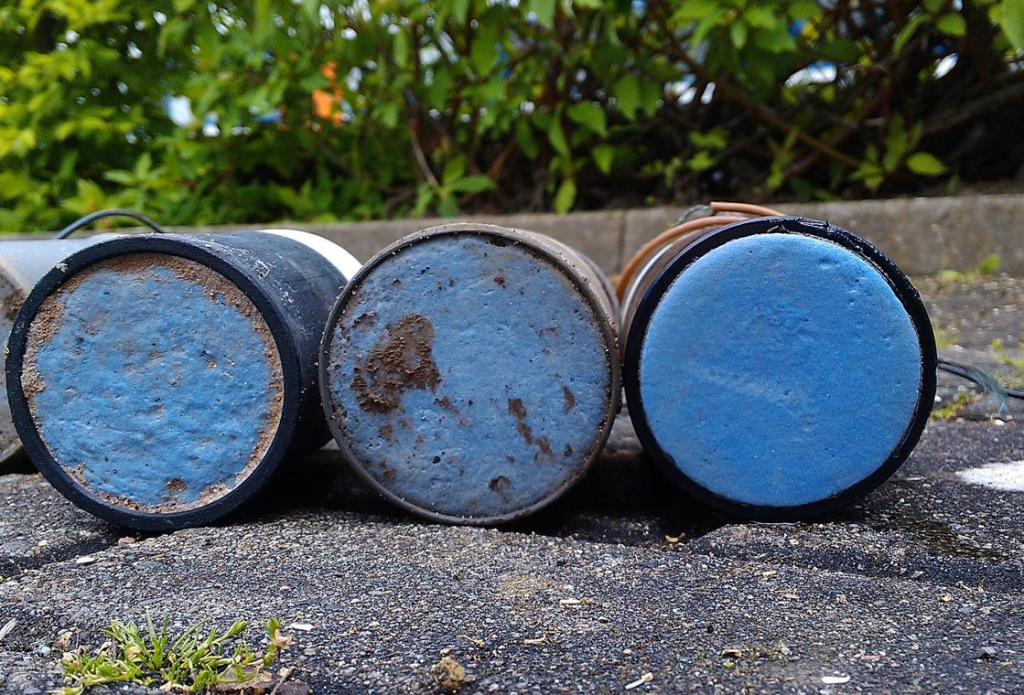
12 months, 8 months, 1 month of usage
Old electrodes will generate a noise floor below 10 Hz. Your MT data becomes unusable!
Storage
Put the cable outside in order to avoid corrosion
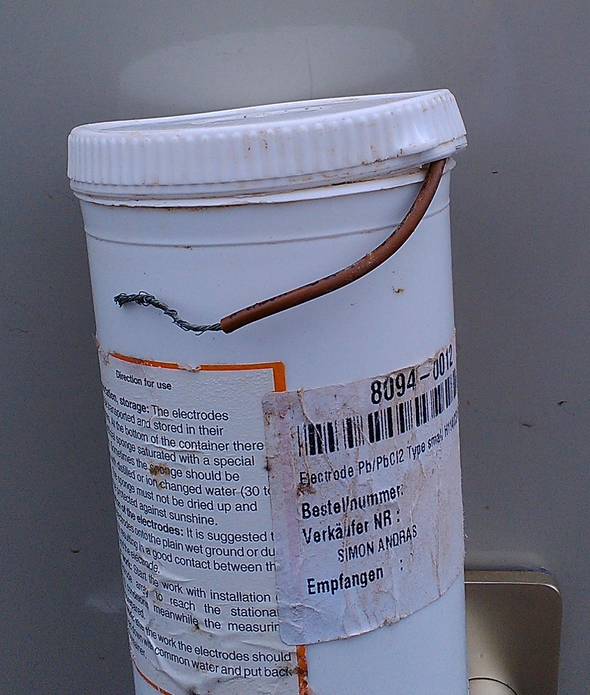
Deployment
You can work without bentonite when the soil is not very dry (here in Germany you normally do not use bentonite).
In dry places you need bentonite.
Bentonite keeps the water, and therefore the electrode keeps wet.
NEVER use salt!
95% of all errors are coming from the electrodes. The deployment of the electrode is the task for the chief.
Electrode Test
Make a pit with 4 electrodes to test. Distance of pit to ADU ca. 10m
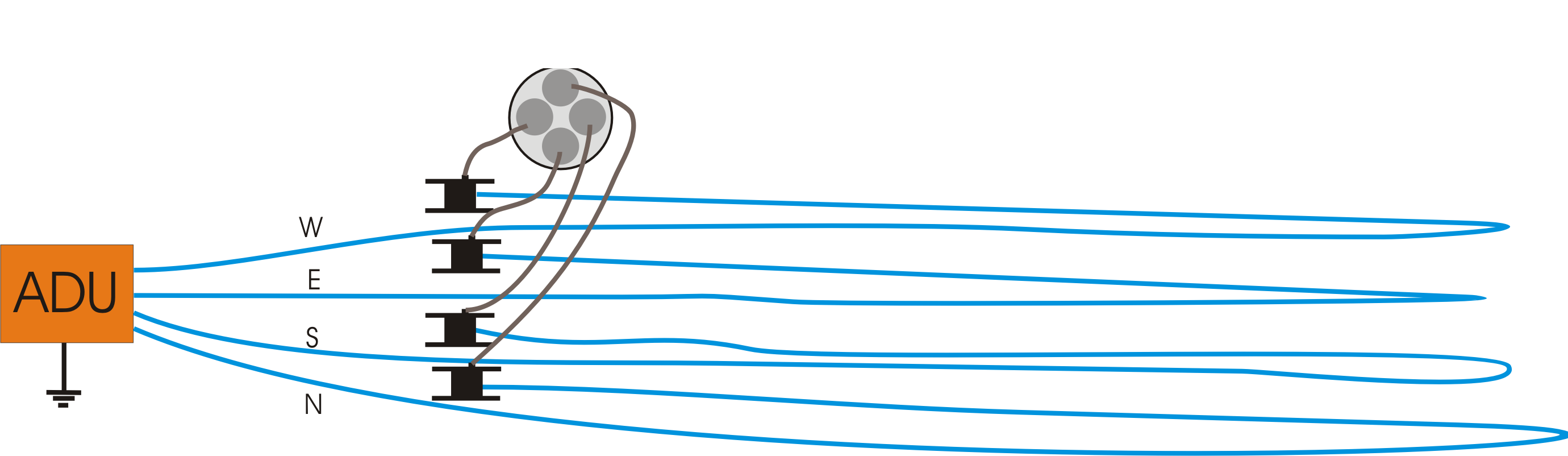
Unreel the wires completely.
Lay out your e-field cables in a way that all cable drums are placed on a location maybe 10 m away from the ADU. The other ends you connect to the ADU.
Ground the ADU as usual.
Use jumper cables to shorten the N/S and E/W cable drums, do not connect the electrodes.
Select a gain of 4 for the first stage.
Make a sounding of maybe 10 minutes with a sampling frequency of 256 Hz. Evaluate the background noise. It will be in the range of less than 100nV/sqrt(Hz). 50/60Hz peaks may be higher. Concentrate on the noise floor.
Next step is to dig a hole for 4 electrodes. All electrodes to be tested shall be in the same pit and close together as shown in the picture. Connect them to the cable drums. Add water, etc. as you do usually.
Repeat the sounding with the same settings, electrodes connected now.
Evaluate the time series and spectra as done before with the shorted inputs. If the electrodes are ok, there should not be a much higher noise floor or jumps in the timeseries or high offset compared to first measurement. In other case the electrodes need to be replaced by new ones.
Like mentioned in other articles: the loss of data is not comparable to the price of fresh electrodes.
Connect FGS or SHFT to ADU-08e
Since one out of 50 where using the multi purpose connector and almost none out of all where using two set of magnetic sensors at the same time, we dropped the multi purpose connector.
With the adapter box [mtx-no 8094-0220-00] you can connect your FGS-03e, FGS-04e and the SHFT-02e to the Hx, Hy and Hz sockets of the ADU-08e
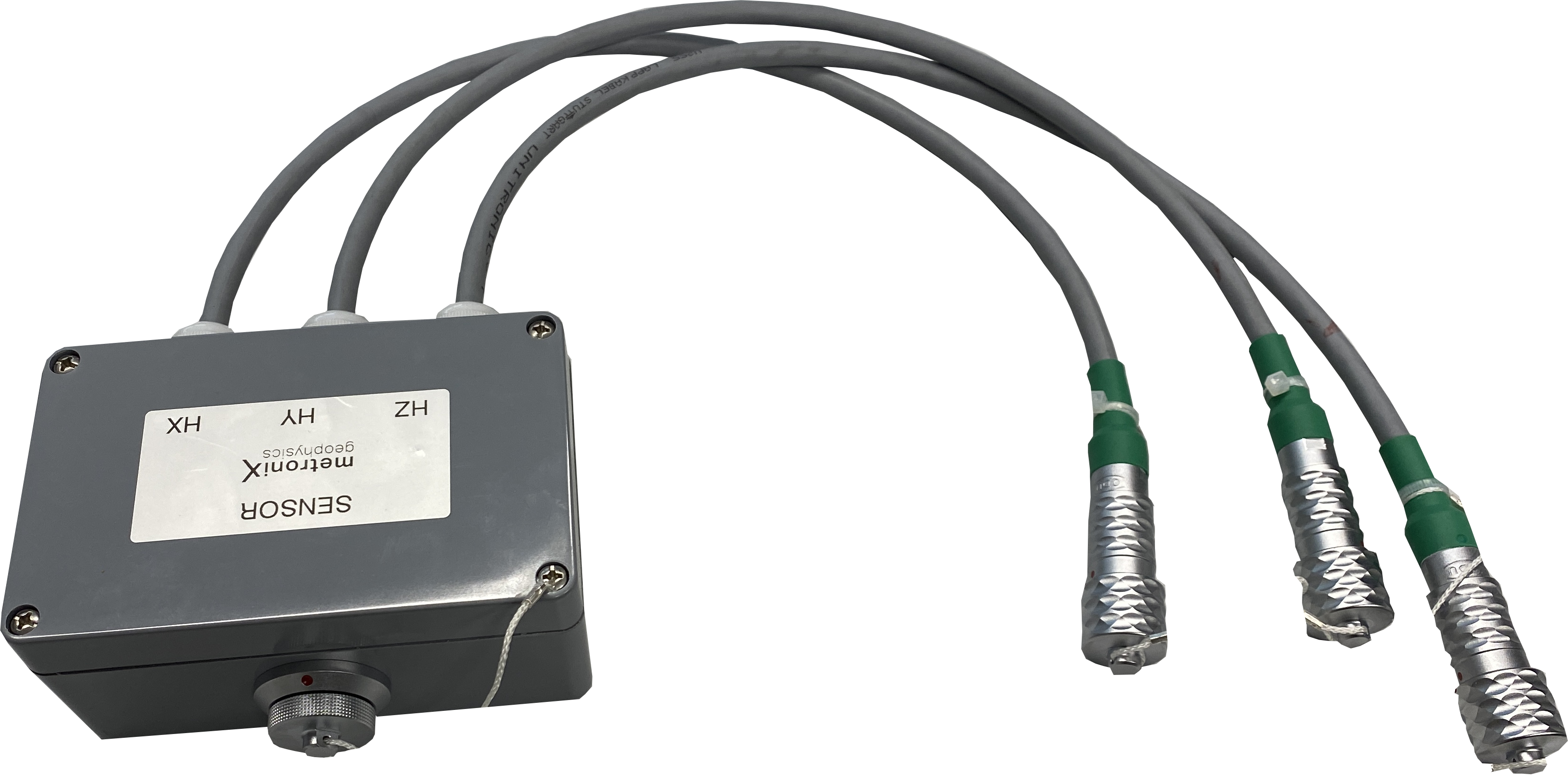
Broken Cores
Inside the coils are magnetic cores in order to amplify the inductance (measured in Henry, H).
The cores are firmly attached to the inner body of the coil - and can’t be replaced individually.
If a core is broken, the inductance is getting too low to measure small magnetic fields. The coil is noisy - but still working.
When a coil comes for repair / refurbishment, first we exchange the pre-amplifier. In almost all cases the pre-amplifier is the source of a malfunctioning coil.
The second step is to measure the inductance - which should be around 180 - 200 H.
In case of a repair, we may try and continue or feedback with the owner of the coil. Decision is then done after field test or before.
The third step is the necessary re-calibration of the coil.
In the calibration facility we use very strong magnetic fields. A broken core may appear here - or may not.
The fourth step is the field test. Here we have normal magnetic fields. And here a broken core should become visible always.
Hence that is does not make sense ot skip steps first, second and third: in case (mostly) the pre-amplifier is damaged you would
sit in the field, ask yourself “pre-amplifier or core?” and proceed to step one.
Possible reasons for the damage:
unqualified personal / low paid personal: they try to crank the coil with a spade in order to get the coil out fast
fallen down from the jeep in the field
during transportation - even maybe by transportation company
The coils are quite robust and the transportation case is safe. But within certain limits. Also pulling out the coil at the cable can cause severe damage.